铝电解电容器铝电极箔的表面处理技术
目录
而在这些电器元件中,铝电解电容器就是功能与金属表面处理技术直接相关的元件之一。す换言之,在以扩大表面积为目的的蚀刻技术、以获得耐高电压电介质皮膜为目的的阳极氧化技术等技术中,与这些技术相关的化学、电化学层面的表面处理是为了有效利用表面处理皮膜的电气特性,这不同于以装饰和防腐蚀为目的的表面处理。
以阳极氧化皮膜为电介质的电解电容器,最初为采用电解质水溶液的湿式电解电容器。而在本世纪初,开发出硼酸铵和甘油组合而成的糊状电解液之后,所谓干式电解电容器随之应运而生,进而铝阳极箔卷绕圆筒状成型的方法也被开发出来,并由此奠定了铝电解电容器小型化与大容量的技术基础。
在此进程中,1956年,由西部电气公司(Western Electric Company)开发出以金属氧化物半导体二氧化锰电解质代替上述糊状电解液的所谓固体电解电容器。此外,以T.C.N.Q.等有机半导体为固体电解质的电容器最近也开始实用化,有了湿式与干式的电解电容器,正在向小型固体电解电容器的方向发展。
这样的发展过程,不仅满足了新时代对于电子电路小型化和高性能化越来越高的要求,电解电容器的性能也必然性地得到了改良和改进。
最近,各种IC、LSI、超LSI,电路越来越小型化,如何在这些电路上搭载电容元件日益成为重要课题,对于表面安装用的贴片型电容器的需求也在激增。
可通过阳极氧化被氧化皮膜覆盖的金属,以“阀金属”之名而广为人知,具体包括铝、钽、铌、钛、铪、锆、锌、钨、铋、锑等,其中在电解电容器中目前实际使用的是铝和钽。
钽在化学上较为稳定,在特性方面也很优秀,然而由于其价格昂贵,目前尚未被广泛采用。廉价且可使用电压范围较广的铝,目前用量最多。电解电容器方面,从全球总产量来看,年增长率与半导体元件大体相同,推测目前的全球月产量可达约50亿个
考虑到如图1所示的平行板电容器,电容C如下式所示。
此处的ε表示电介质的介电常数,S表示电介质的表面积[cm2],d则表示电介质的厚度[cm]。要通过上述算式获得更大的电容C,就需要更大的介电常数、更大的面积、以及更薄的电介质厚度。
而将铝或钽阳极氧化后所获得的氧化铝(Al2O3)或氧化钽(Ta2O5)皮膜的ε分别为8~9或约25,数值并不算大。但是如后文所述,可以用适当的电解液进行阳极氧化,从而获得既耐高电压又极薄的皮膜。此外还可以通过蚀刻处理或使用多孔烧结体来扩大表面积。
因此与以往的电容器相比,铝电解电容器体积小、价格便宜,却又可获得大容量,符合近年来元件小型化的要求,因此作为大容量电容器得以广泛普及。
图2に为目前普遍采用的各种电容器所使用的容量范围。从此图2中可知,铝电解电容器可覆盖大容量范围。
图3为铝电解电容器的原理模型图。通过阳极氧化所获得的皮膜厚度(d),可根据阳极氧化时所施加的电压进行自由调节。
换言之,铝电解电容器的特点是,可根据阳极氧化电压调整容量;所生成皮膜具有不放出一定方向电流(正方向)的性质(阀作用),因此有极性;由于内置电解质,电容器本身具有皮膜修复性等。
要求电解电容器具备的主要电气特性包括以下三点。
(1)静电容量及其公差
通常120Hz的容量以μF表示,其公差逐渐变小,一般为±20%或±10%。
(2)漏电流
电介质皮膜的绝缘性非常高,但也并未无限高。施加直流电压时,或多或少会有漏电流流过。如果此数值较大,会影响设备的性能、寿命、可靠性,因此其理想值应足够小,对于其变化率也开始有了规定。
(3)串联电阻
除实际不存在的理想电容器之外,所有电容器的内部都有等效串联电阻。换言之,在理想电容器中,电流相位比电位高90°,然而实际上则会产生延迟(该延迟的角度称为介电损耗角),产生与电压同相的电流,并在电容器内部作为功率被消耗(图4)。通常以介电损耗角δ的正切tanδ表示其尺度,称之为介电损耗因子(Dielectric dissipation factor)。在交流电路中,尤其是需要用到高频、高电压、大容量时,该电阻部分直接影响电容器的发热量,因此可谓之与寿命最为相关的重要电气特性之一。
对电容器电气特性构成影响的使用条件,包括电路电压、纹波电流、温度、频率、时间等。上述电气特性会根据各自的条件而产生很大的变化。因此,可使用的温度范围、电压(直流、交流)、适用频率范围等受限。要获得稳定性更高的电容器,就需要研究作为材质的铝材料、蚀刻条件、阳极氧化条件、电解液的构成、元件结构、封口结构等。从表面处理技术的立场来看,铝电解电容器的制造与上述各种电气特性相关,并且尤其重视以下两点技术领域。
i)用于扩大单位面积容量的蚀刻相关技术
ii)用于获得稳定电介质皮膜的阳极氧化相关技术
而用硼酸铵等接近中性的电解液阳极氧化铝时生成的皮膜,则被称为阻隔皮膜。该阻隔皮膜的厚度为1μm以下,非常薄且致密,具有106~107数量级V/cm的高绝缘耐压性。可有效阻止电流,因此也被称为绝缘皮膜等,用作电解电容器的电介质皮膜。
以电解电容器为对象的电介质皮膜,无论是钽的Ta2O5,还是铝的Al2O3,都是非常薄且致密的阻隔皮膜。在这样的高电场中,关于皮膜中所流离子电流i与电场强度E之间的关系,Guntherschultze与Betz遵循指数法则研究出算式(1)。
i=AexpBE (1)
A=A'exp(-W/kT)、B=B'/kT,还包括离子电流i的温度依赖性。算式(1)与后述的金属~氧化物界面为律速(决定化学反应速度的最主要因素)假定下所衍生的Cabrera~Mott的理论式,以及以氧化物内律速为前提所衍生的Verway的理论式一致,因此可认为找到了理论依据。
考虑到恒定电流下的皮膜生长速度,皮膜厚度的增加速度如算式(2)所示。
dD/dt=iM/zFρ (2)
此处D为皮膜厚度,t为时间,i为离子电流密度,Z为分子量,M为生成氧化物1g分子量所需的法拉第数,ρ为皮膜密度。
在一定离子电流密度下,即使氧化膜的厚度增加,微分电场强度Ed(=dV/dD)也只会发生微小的变化。如果将其设为恒定,则电位的增加速度如算式(3)所示。
dⅤ/dt=Ed・i・M/zFρ (3)
换言之,生长速度与离子电流成正比。此外,由于皮膜中的电场强度没有变化,以恒定电流密度进行阳极氧化时,电压会随时间而直线上升。另一方面,考虑到恒定电压下的皮膜生长,在恒定电压下,Ed会随着皮膜的生长而减少,因此离子电流也会随之减少。而电场的减少速度也会随之变小,因此电流的减少速度也会随之降低。因此,由于生长速度变得极慢,实际上皮膜厚度可以说达到了某个极限值,因此使用“Å/V”来进行表达。
然而,如果在恒定电流下无限持续阳极氧化,则如算式(3)所示,蚀刻浴电压也会随之无限上升。而实际的数值是有界限的,在达到依赖于阳极金属和化成液的种类、液浓度、电流密度等的某个电压值之后,即使再继续进行化成,电压也不会继续随之上升。
其原因是,由离子导电生成皮膜,转变为电子导电皮膜绝缘破坏,导致无法正常生成皮膜。实际上,在达到该极大破坏电压值之前,皮膜生成速度就已经变慢,从阳极面产生火花,不久后就会达到破坏电压水准(図5)。产生该火花的电压称为火花电压,而测量该火花电压之后,也可将其用作判断阳极材料好坏的试验方法。可阳极氧化的电压范围:铝箔为约800V,钽箔为约400V左右。
此外,阳极氧化皮膜厚度与阳极氧化电压成正比,而静电容量则与电介质皮膜厚度成反比,因此,箔则按面积、粉末则按重量,(电容C)×(化成电压V)≈恒定关系近似成立。
图6 为铝电解电容器制造工序的一例。
(1)铝箔
作为阳极的铝箔,使用宽度为500mm、厚度为0.05~0.1mm左右的卷取型产品。铝的纯度为4N(99.99%)左右,杂质的主要成分为硅、铁、铜、镁、锌等,根据用途按软质、硬质(后述)区分使用。所含杂质的种类和数量,将在蚀刻工序中对蚀刻坑的形状和倍率构成较大影响,此外还会对阳极氧化皮膜的漏电流构成影响,进而大幅影响产品寿命。阴极用一般采用2N左右的铝箔。图7为蚀刻工序的一例。
(2)预处理
以箔脱脂或去除自然氧化皮膜等为目的,进行使表面状态均匀化的预处理。方法一般为三氯乙烯脱脂、温或冷碱清洗、无机酸处理或交流或阴极电解清洗,结束后充分水洗。
(3)蚀刻
为了在同一面积下获得尽可能大的表面积,而对铝箔表面进行扩倍的工序,与容量直接相关,因此是非常重要的一道工序。该工序也有化学方法等,然而从倍率、管理难度等方面来看,一般性采用的方法是电化学蚀刻。蚀刻浴主要使用盐酸、食盐等氯化物水溶液,而电源则可以采用直流、交流、直交流交替或叠加等方式。作为占主导地位的反应,氯化物水溶液采用如下算式进行表示。
Al+3Cl-→AlCl3+3e
影响倍率的因素包括温度、蚀刻浴浓度、pH值、电流密度、通电量、电极结构等,而如果倍率因箔的宽度方向和长度方向而异,则在该蚀刻工序之后所进行的阳极氧化工序后,为用于电容器元件而将箔裁剪成规定尺寸时会导致容量出现偏差,因此避免让倍率因宽度方向和长度方向而产生偏差,是最为重要的管理项目。
而蚀刻处理后进行的阳极氧化,所生成的阳极氧化皮膜的厚度则因阳极氧化电压的高低(通常为5V~700V的范围内)而异。因此,需要根据阳极氧化电压来控制蚀刻形状。
如图8所示,(A)为已被蚀刻的状态,(B)为已在其表面进行低压化成的情况,(C)为已在同一表面进行高压化成的情况。 在案例(C)中,尽管费力通过蚀刻扩大了表面积,其效果也未得到体现,无法大幅获取容量。因此需要为高压用途而打开较大的孔。
由于此种理由,蚀刻处理的过程中,一般会根据之后的阳极氧化处理时的阳极氧化电压的高低,将蚀刻条件分为高压用、低压用两种或高压用、中压用、低压用三种。
低压用途时,为获得细小的蚀刻孔,使用硬质箔进行直流蚀刻,或使用硬质或软质箔进行交流蚀刻。由于蚀刻机制不同,直流电蚀刻会生长出微细壁孔沟,而交流电蚀刻则会生长出微细立方体坑。
在交流蚀刻的过程中,蚀刻从箔的两面向深度方向均匀进行,因此残留铝芯得以保持均匀,让箔保持较高的强度(照片1)。在低压用的小型铝电解电容器中,所用箔的宽度非常窄,因此主要使用此类强度较强的交流蚀刻箔。
而高压用途则使用统一结晶方位的软质箔进行直流蚀刻,使粗孔径的壁孔沟向深度方向排列进行蚀刻(照片2)。照片1、2中的试料,均为在蚀刻后进行阳极氧化的基础上,不溶解氧化皮膜而只溶解底层铝,清晰地展示了蚀刻层和蚀刻坑的形状。
蚀刻处理后,用硝酸等进行纯化和处理,充分进行纯水清洗后,干燥并卷取,以去除电解时箔表面所产生的粉状铝以及蚀刻时所产生的氯离子和表面杂质。为确保铝电解电容器的长寿命和高可靠性,氯离子是尤其绝对要避免的污染物。因此,需要通过冲洗、超声波清洗等方式进行充分冲洗。此外,蚀刻后的铝箔表面为活性,因此在保管箔时需要多加注意。由此可见,已蚀刻箔的倍率(与原箔的表面积相比较),低压用途为约100倍,高压用途为约20倍。
(4)阳极氧化
在形成电容器电介质--氧化皮膜的工序中,以在前工序中被蚀刻并扩大表面积的铝箔卷取品为阳极,连续进行阳极氧化。图9为连续阳极氧化工序的一例。
电解液使用硼酸铵、磷酸铵、有机酸氨等缓冲溶液,以电容器额定电压(通常为6.3V~500V)的140~160%的电压进行阳极氧化。
作业分为一阶段方式和多阶段方式,前者为阳极氧化电压在100V左右以下的情况,而高压阳极氧化时则需要分为二~三个阶段依次提高阳极氧化电压。进行高压阳极氧化时,通常在进行阳极氧化之前,在纯水中煮沸,在最外表面形成模拟勃姆石(一水软铝石)皮膜(AlOOH)。该方法的优点包括,可在获得耐高电压的结晶性皮膜的同时降低功耗、加快处理速度等(照片3、照片4)。在漏电流变得足够小之前,阳极氧化处理后的箔经水洗、干燥后卷取。
阳极氧化工序结束后,经每单位面积容量检查后,分别切割成所需的尺寸,安装引线,在与对置阴极箔之间插入隔膜纸,制作卷绕元件。隔膜纸不仅可以避免阳极箔和阴极箔产生机械接触,同时还承担着浸渍保持电解液的作用。
(5)电解液的浸渍
将电解液浸渍到卷绕元件中。以乙二醇、甘油等多元醇类为主要溶剂,并在溶液中溶解硼酸铵或有机酸铵盐等不侵蚀铝的电解质而形成电解液。电解液的配方能够确保使其具有皮膜修复性且具有适度的电阻,常温下为糊状。电解液的组成,对前述的电容器中所要求的三大电气特性--温度特性、频率特性、产品寿命等有较大影响,是重要探讨项目。
将该电解质置于100~130℃的高温下降低其粘度,将卷绕元件真空浸渍或深度浸渍,使两电极箔的表面完全被电解液覆盖。浸渍的元件被封入铝外壳中之后成为成品。以在切割时的切口面形成皮膜,以及修复卷绕时机械变形所导致的皮膜龟裂等为目的,在产品已基本完成的状态下再次用高温施加电压进行蚀刻,充分减小漏电流后,成为铝电解电容器的成品。
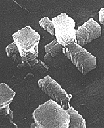
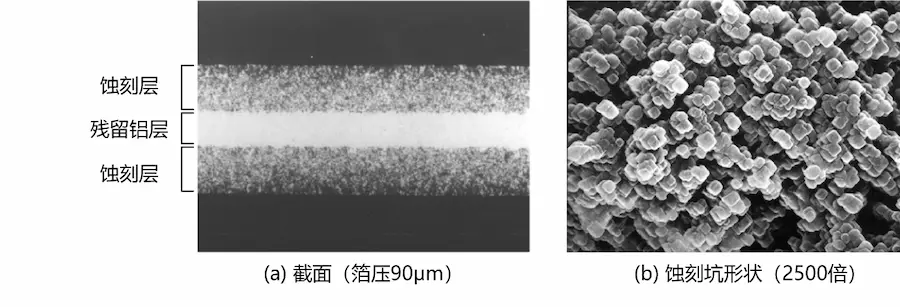
【照片1】低压用交流蚀刻后,再经阳极氧化处理的阳极箔
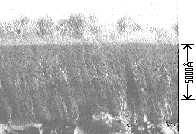
【照片4】经阳极氧化后的皮膜 (Composite anodic oxide film)
1. 前言
近年来电子设备类迅猛发展,以用于电子设备电路的集成电路、半导体元件、电子管等为代表的有源元件,以L、C、R等为代表的无源元件,以及功能性元件、机构性元件类等,都在小型化、高性能化、高可靠化方面取得了较大的发展。而在这些电器元件中,铝电解电容器就是功能与金属表面处理技术直接相关的元件之一。す换言之,在以扩大表面积为目的的蚀刻技术、以获得耐高电压电介质皮膜为目的的阳极氧化技术等技术中,与这些技术相关的化学、电化学层面的表面处理是为了有效利用表面处理皮膜的电气特性,这不同于以装饰和防腐蚀为目的的表面处理。
以阳极氧化皮膜为电介质的电解电容器,最初为采用电解质水溶液的湿式电解电容器。而在本世纪初,开发出硼酸铵和甘油组合而成的糊状电解液之后,所谓干式电解电容器随之应运而生,进而铝阳极箔卷绕圆筒状成型的方法也被开发出来,并由此奠定了铝电解电容器小型化与大容量的技术基础。
在此进程中,1956年,由西部电气公司(Western Electric Company)开发出以金属氧化物半导体二氧化锰电解质代替上述糊状电解液的所谓固体电解电容器。此外,以T.C.N.Q.等有机半导体为固体电解质的电容器最近也开始实用化,有了湿式与干式的电解电容器,正在向小型固体电解电容器的方向发展。
这样的发展过程,不仅满足了新时代对于电子电路小型化和高性能化越来越高的要求,电解电容器的性能也必然性地得到了改良和改进。
最近,各种IC、LSI、超LSI,电路越来越小型化,如何在这些电路上搭载电容元件日益成为重要课题,对于表面安装用的贴片型电容器的需求也在激增。
2. 铝电解电容器
电解电容器(Electrolytic capacitor)的原理是,通过阳极氧化在金属表面形成电介质氧化皮膜,使其与电解液、高粘度电解液或固体电解质(Electrolyte)接触,并使其在与对电极之间的位置蓄积电荷。可通过阳极氧化被氧化皮膜覆盖的金属,以“阀金属”之名而广为人知,具体包括铝、钽、铌、钛、铪、锆、锌、钨、铋、锑等,其中在电解电容器中目前实际使用的是铝和钽。
钽在化学上较为稳定,在特性方面也很优秀,然而由于其价格昂贵,目前尚未被广泛采用。廉价且可使用电压范围较广的铝,目前用量最多。电解电容器方面,从全球总产量来看,年增长率与半导体元件大体相同,推测目前的全球月产量可达约50亿个
考虑到如图1所示的平行板电容器,电容C如下式所示。
此处的ε表示电介质的介电常数,S表示电介质的表面积[cm2],d则表示电介质的厚度[cm]。要通过上述算式获得更大的电容C,就需要更大的介电常数、更大的面积、以及更薄的电介质厚度。
而将铝或钽阳极氧化后所获得的氧化铝(Al2O3)或氧化钽(Ta2O5)皮膜的ε分别为8~9或约25,数值并不算大。但是如后文所述,可以用适当的电解液进行阳极氧化,从而获得既耐高电压又极薄的皮膜。此外还可以通过蚀刻处理或使用多孔烧结体来扩大表面积。
因此与以往的电容器相比,铝电解电容器体积小、价格便宜,却又可获得大容量,符合近年来元件小型化的要求,因此作为大容量电容器得以广泛普及。
图2に为目前普遍采用的各种电容器所使用的容量范围。从此图2中可知,铝电解电容器可覆盖大容量范围。
图3为铝电解电容器的原理模型图。通过阳极氧化所获得的皮膜厚度(d),可根据阳极氧化时所施加的电压进行自由调节。
换言之,铝电解电容器的特点是,可根据阳极氧化电压调整容量;所生成皮膜具有不放出一定方向电流(正方向)的性质(阀作用),因此有极性;由于内置电解质,电容器本身具有皮膜修复性等。
要求电解电容器具备的主要电气特性包括以下三点。
(1)静电容量及其公差
通常120Hz的容量以μF表示,其公差逐渐变小,一般为±20%或±10%。
(2)漏电流
电介质皮膜的绝缘性非常高,但也并未无限高。施加直流电压时,或多或少会有漏电流流过。如果此数值较大,会影响设备的性能、寿命、可靠性,因此其理想值应足够小,对于其变化率也开始有了规定。
(3)串联电阻
除实际不存在的理想电容器之外,所有电容器的内部都有等效串联电阻。换言之,在理想电容器中,电流相位比电位高90°,然而实际上则会产生延迟(该延迟的角度称为介电损耗角),产生与电压同相的电流,并在电容器内部作为功率被消耗(图4)。通常以介电损耗角δ的正切tanδ表示其尺度,称之为介电损耗因子(Dielectric dissipation factor)。在交流电路中,尤其是需要用到高频、高电压、大容量时,该电阻部分直接影响电容器的发热量,因此可谓之与寿命最为相关的重要电气特性之一。
对电容器电气特性构成影响的使用条件,包括电路电压、纹波电流、温度、频率、时间等。上述电气特性会根据各自的条件而产生很大的变化。因此,可使用的温度范围、电压(直流、交流)、适用频率范围等受限。要获得稳定性更高的电容器,就需要研究作为材质的铝材料、蚀刻条件、阳极氧化条件、电解液的构成、元件结构、封口结构等。从表面处理技术的立场来看,铝电解电容器的制造与上述各种电气特性相关,并且尤其重视以下两点技术领域。
i)用于扩大单位面积容量的蚀刻相关技术
ii)用于获得稳定电介质皮膜的阳极氧化相关技术
3. 铝阳极氧化电介质皮膜
氧化铝皮膜是一种较为有名的铝阳极氧化皮膜。此种皮膜可以在高电场下让铝更易溶解于电解液中。例如,可通过在硫酸、铬酸、草酸等电解液中阳极氧化获得。此皮膜为多孔质,可以长厚至10μm~100μm。此外,还可以用作铝制窗框等的防腐蚀、着色皮膜。而用硼酸铵等接近中性的电解液阳极氧化铝时生成的皮膜,则被称为阻隔皮膜。该阻隔皮膜的厚度为1μm以下,非常薄且致密,具有106~107数量级V/cm的高绝缘耐压性。可有效阻止电流,因此也被称为绝缘皮膜等,用作电解电容器的电介质皮膜。
以电解电容器为对象的电介质皮膜,无论是钽的Ta2O5,还是铝的Al2O3,都是非常薄且致密的阻隔皮膜。在这样的高电场中,关于皮膜中所流离子电流i与电场强度E之间的关系,Guntherschultze与Betz遵循指数法则研究出算式(1)。
i=AexpBE (1)
A=A'exp(-W/kT)、B=B'/kT,还包括离子电流i的温度依赖性。算式(1)与后述的金属~氧化物界面为律速(决定化学反应速度的最主要因素)假定下所衍生的Cabrera~Mott的理论式,以及以氧化物内律速为前提所衍生的Verway的理论式一致,因此可认为找到了理论依据。
考虑到恒定电流下的皮膜生长速度,皮膜厚度的增加速度如算式(2)所示。
dD/dt=iM/zFρ (2)
此处D为皮膜厚度,t为时间,i为离子电流密度,Z为分子量,M为生成氧化物1g分子量所需的法拉第数,ρ为皮膜密度。
在一定离子电流密度下,即使氧化膜的厚度增加,微分电场强度Ed(=dV/dD)也只会发生微小的变化。如果将其设为恒定,则电位的增加速度如算式(3)所示。
dⅤ/dt=Ed・i・M/zFρ (3)
换言之,生长速度与离子电流成正比。此外,由于皮膜中的电场强度没有变化,以恒定电流密度进行阳极氧化时,电压会随时间而直线上升。另一方面,考虑到恒定电压下的皮膜生长,在恒定电压下,Ed会随着皮膜的生长而减少,因此离子电流也会随之减少。而电场的减少速度也会随之变小,因此电流的减少速度也会随之降低。因此,由于生长速度变得极慢,实际上皮膜厚度可以说达到了某个极限值,因此使用“Å/V”来进行表达。
然而,如果在恒定电流下无限持续阳极氧化,则如算式(3)所示,蚀刻浴电压也会随之无限上升。而实际的数值是有界限的,在达到依赖于阳极金属和化成液的种类、液浓度、电流密度等的某个电压值之后,即使再继续进行化成,电压也不会继续随之上升。
其原因是,由离子导电生成皮膜,转变为电子导电皮膜绝缘破坏,导致无法正常生成皮膜。实际上,在达到该极大破坏电压值之前,皮膜生成速度就已经变慢,从阳极面产生火花,不久后就会达到破坏电压水准(図5)。产生该火花的电压称为火花电压,而测量该火花电压之后,也可将其用作判断阳极材料好坏的试验方法。可阳极氧化的电压范围:铝箔为约800V,钽箔为约400V左右。
此外,阳极氧化皮膜厚度与阳极氧化电压成正比,而静电容量则与电介质皮膜厚度成反比,因此,箔则按面积、粉末则按重量,(电容C)×(化成电压V)≈恒定关系近似成立。
4. 铝电极箔以及铝电解电容器的制造方法
電电解电容器的种类,可按阳极体的种类分为铝和钽,也可按阳极体的形状分为箔型和烧结型等,此外还可以按电解质的种类,分为使用糊状电解液的干式与使用氧化物半导体的固体型等。这里将以铝电极箔的表面处理为中心,介绍最具代表性的、使用铝箔的铝干式电解电容器的制造方法。图6 为铝电解电容器制造工序的一例。
(1)铝箔
作为阳极的铝箔,使用宽度为500mm、厚度为0.05~0.1mm左右的卷取型产品。铝的纯度为4N(99.99%)左右,杂质的主要成分为硅、铁、铜、镁、锌等,根据用途按软质、硬质(后述)区分使用。所含杂质的种类和数量,将在蚀刻工序中对蚀刻坑的形状和倍率构成较大影响,此外还会对阳极氧化皮膜的漏电流构成影响,进而大幅影响产品寿命。阴极用一般采用2N左右的铝箔。图7为蚀刻工序的一例。
(2)预处理
以箔脱脂或去除自然氧化皮膜等为目的,进行使表面状态均匀化的预处理。方法一般为三氯乙烯脱脂、温或冷碱清洗、无机酸处理或交流或阴极电解清洗,结束后充分水洗。
(3)蚀刻
为了在同一面积下获得尽可能大的表面积,而对铝箔表面进行扩倍的工序,与容量直接相关,因此是非常重要的一道工序。该工序也有化学方法等,然而从倍率、管理难度等方面来看,一般性采用的方法是电化学蚀刻。蚀刻浴主要使用盐酸、食盐等氯化物水溶液,而电源则可以采用直流、交流、直交流交替或叠加等方式。作为占主导地位的反应,氯化物水溶液采用如下算式进行表示。
Al+3Cl-→AlCl3+3e
影响倍率的因素包括温度、蚀刻浴浓度、pH值、电流密度、通电量、电极结构等,而如果倍率因箔的宽度方向和长度方向而异,则在该蚀刻工序之后所进行的阳极氧化工序后,为用于电容器元件而将箔裁剪成规定尺寸时会导致容量出现偏差,因此避免让倍率因宽度方向和长度方向而产生偏差,是最为重要的管理项目。
而蚀刻处理后进行的阳极氧化,所生成的阳极氧化皮膜的厚度则因阳极氧化电压的高低(通常为5V~700V的范围内)而异。因此,需要根据阳极氧化电压来控制蚀刻形状。
如图8所示,(A)为已被蚀刻的状态,(B)为已在其表面进行低压化成的情况,(C)为已在同一表面进行高压化成的情况。 在案例(C)中,尽管费力通过蚀刻扩大了表面积,其效果也未得到体现,无法大幅获取容量。因此需要为高压用途而打开较大的孔。
由于此种理由,蚀刻处理的过程中,一般会根据之后的阳极氧化处理时的阳极氧化电压的高低,将蚀刻条件分为高压用、低压用两种或高压用、中压用、低压用三种。
低压用途时,为获得细小的蚀刻孔,使用硬质箔进行直流蚀刻,或使用硬质或软质箔进行交流蚀刻。由于蚀刻机制不同,直流电蚀刻会生长出微细壁孔沟,而交流电蚀刻则会生长出微细立方体坑。
在交流蚀刻的过程中,蚀刻从箔的两面向深度方向均匀进行,因此残留铝芯得以保持均匀,让箔保持较高的强度(照片1)。在低压用的小型铝电解电容器中,所用箔的宽度非常窄,因此主要使用此类强度较强的交流蚀刻箔。
而高压用途则使用统一结晶方位的软质箔进行直流蚀刻,使粗孔径的壁孔沟向深度方向排列进行蚀刻(照片2)。照片1、2中的试料,均为在蚀刻后进行阳极氧化的基础上,不溶解氧化皮膜而只溶解底层铝,清晰地展示了蚀刻层和蚀刻坑的形状。
蚀刻处理后,用硝酸等进行纯化和处理,充分进行纯水清洗后,干燥并卷取,以去除电解时箔表面所产生的粉状铝以及蚀刻时所产生的氯离子和表面杂质。为确保铝电解电容器的长寿命和高可靠性,氯离子是尤其绝对要避免的污染物。因此,需要通过冲洗、超声波清洗等方式进行充分冲洗。此外,蚀刻后的铝箔表面为活性,因此在保管箔时需要多加注意。由此可见,已蚀刻箔的倍率(与原箔的表面积相比较),低压用途为约100倍,高压用途为约20倍。
(4)阳极氧化
在形成电容器电介质--氧化皮膜的工序中,以在前工序中被蚀刻并扩大表面积的铝箔卷取品为阳极,连续进行阳极氧化。图9为连续阳极氧化工序的一例。
电解液使用硼酸铵、磷酸铵、有机酸氨等缓冲溶液,以电容器额定电压(通常为6.3V~500V)的140~160%的电压进行阳极氧化。
作业分为一阶段方式和多阶段方式,前者为阳极氧化电压在100V左右以下的情况,而高压阳极氧化时则需要分为二~三个阶段依次提高阳极氧化电压。进行高压阳极氧化时,通常在进行阳极氧化之前,在纯水中煮沸,在最外表面形成模拟勃姆石(一水软铝石)皮膜(AlOOH)。该方法的优点包括,可在获得耐高电压的结晶性皮膜的同时降低功耗、加快处理速度等(照片3、照片4)。在漏电流变得足够小之前,阳极氧化处理后的箔经水洗、干燥后卷取。
阳极氧化工序结束后,经每单位面积容量检查后,分别切割成所需的尺寸,安装引线,在与对置阴极箔之间插入隔膜纸,制作卷绕元件。隔膜纸不仅可以避免阳极箔和阴极箔产生机械接触,同时还承担着浸渍保持电解液的作用。
(5)电解液的浸渍
将电解液浸渍到卷绕元件中。以乙二醇、甘油等多元醇类为主要溶剂,并在溶液中溶解硼酸铵或有机酸铵盐等不侵蚀铝的电解质而形成电解液。电解液的配方能够确保使其具有皮膜修复性且具有适度的电阻,常温下为糊状。电解液的组成,对前述的电容器中所要求的三大电气特性--温度特性、频率特性、产品寿命等有较大影响,是重要探讨项目。
将该电解质置于100~130℃的高温下降低其粘度,将卷绕元件真空浸渍或深度浸渍,使两电极箔的表面完全被电解液覆盖。浸渍的元件被封入铝外壳中之后成为成品。以在切割时的切口面形成皮膜,以及修复卷绕时机械变形所导致的皮膜龟裂等为目的,在产品已基本完成的状态下再次用高温施加电压进行蚀刻,充分减小漏电流后,成为铝电解电容器的成品。
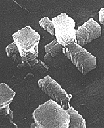
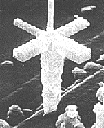
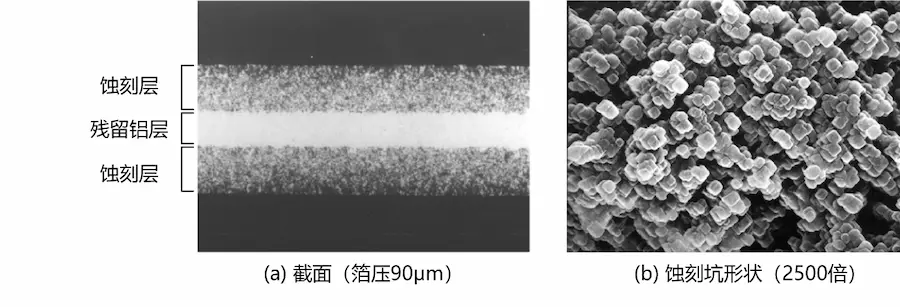
【照片1】低压用交流蚀刻后,再经阳极氧化处理的阳极箔
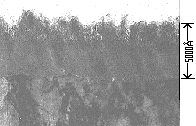
【照片3】阳极氧化前进行纯水煮沸处理后的皮膜 (Pseudo-boehmite film)
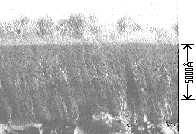
【照片4】经阳极氧化后的皮膜 (Composite anodic oxide film)
上述内容以外的问题及咨询,联系方式如下。